3PE Anti-Corrosion Steel Pipe | 3PE Coating
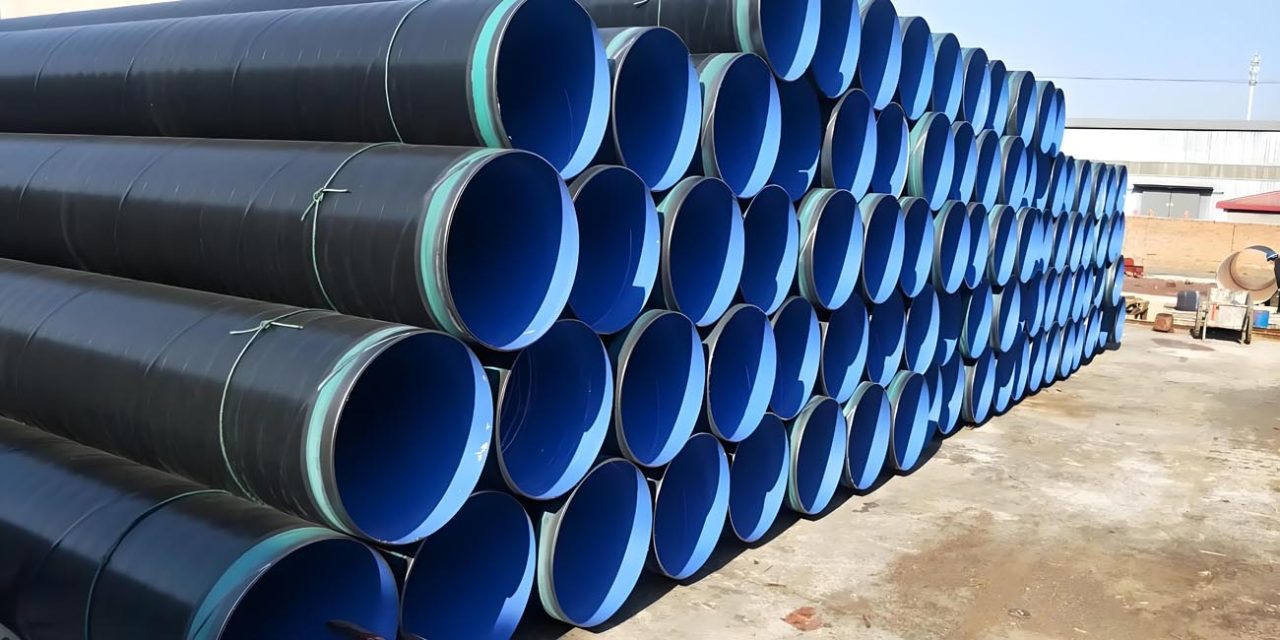
3PE Anti-Corrosion Steel Pipe
3PE (Three-layer Polyethylene) anti-corrosion steel pipes are widely used in various industries for their excellent corrosion resistance and durability. This type of steel pipe is commonly used in oil and gas pipelines, water supply systems, and other applications where long-term exposure to harsh environments is expected.
Structure and Composition of 3PE Coating
The 3PE coating system consists of three layers:
- Fusion Bonded Epoxy (FBE) Layer: This inner layer is applied directly to the steel pipe surface. It provides excellent adhesion to the steel substrate and acts as the primary corrosion barrier.
- Adhesive Layer: This intermediate layer ensures a strong bond between the FBE layer and the outer polyethylene layer. It is typically made from a copolymer adhesive.
- Polyethylene (PE) Layer: The outermost layer provides mechanical protection against physical damage and environmental impact. It is made from high-density polyethylene (HDPE), which offers excellent resistance to abrasion and UV radiation.
Advantages of 3PE Anti-Corrosion Coating
- Superior Corrosion Resistance: The combination of FBE and PE provides outstanding protection against corrosion, making it suitable for use in harsh environments.
- Excellent Mechanical Properties: The PE layer offers high resistance to physical damage, such as abrasion and impact, ensuring the integrity of the pipeline during handling, transportation, and installation.
- Long Service Life: The 3PE coating extends the service life of the steel pipe, reducing maintenance costs and downtime.
- Strong Adhesion: The adhesive layer ensures a strong bond between the FBE and PE layers, preventing delamination and ensuring long-lasting protection.
- Chemical Resistance: The 3PE coating is resistant to a wide range of chemicals, making it suitable for use in various industrial applications.
Application Process of 3PE Coating
The application of the 3PE coating involves several steps to ensure a high-quality, durable finish:
- Surface Preparation: The steel pipe is thoroughly cleaned to remove any rust, scale, or contaminants. This is typically done through abrasive blasting to achieve a clean, rough surface that promotes good adhesion.
- FBE Application: The fusion bonded epoxy layer is applied to the heated steel pipe. The epoxy powder melts and flows to form a uniform coating that bonds to the steel surface.
- Adhesive Layer Application: The copolymer adhesive is applied over the FBE layer while it is still hot. This ensures a strong bond between the epoxy and the outer polyethylene layer.
- Polyethylene Layer Application: The polyethylene layer is extruded over the adhesive layer, forming the outer protective coating. The pipe is then cooled to solidify the PE layer and complete the coating process.
Applications of 3PE Anti-Corrosion Steel Pipes
3PE anti-corrosion steel pipes are used in a variety of industries and applications, including:
- Oil and Gas Pipelines: Transporting crude oil, natural gas, and refined products over long distances.
- Water Supply Systems: Carrying potable water and wastewater in municipal and industrial water systems.
- Chemical Processing: Handling corrosive chemicals and fluids in chemical plants.
- Marine and Offshore: Pipelines in coastal and offshore environments where exposure to saltwater and harsh conditions is common.
- Underground Pipelines: Buried pipelines in various industries, providing durable protection against soil and environmental factors.
Anticorrosive Pipe
Overview
3PE (Three-layer Polyethylene) coating pipes, also known as 3PE anticorrosive pipes, are designed for applications requiring robust protection against corrosion and mechanical damage. These pipes are commonly used in industries such as coal mining, power plants, and oil and gas transmission.
Product Specifications
Application
- Industries: Coal mine, heat and power plant, oil and gas transmission
- Function: Provides excellent corrosion resistance and mechanical protection for pipelines in harsh environments.
Standards
- DIN 30670
- CAN/CSA-Z245.21
- NFA 49-710
- ISO DIS21809-1
Size Range
- Diameter: DN50 to DN2200
Coating Layers
- Layer 1: Epoxy Powder
- Thickness: ≥80 µm
- Function: Provides excellent adhesion and primary corrosion barrier.
- Layer 2: Adhesive
- Thickness: 170-250 µm
- Function: Ensures strong bonding between the epoxy powder and polyethylene layers.
- Layer 3: Polyethylene
- Thickness: 1.8-3.7 mm
- Function: Offers mechanical protection against physical damage and environmental impact.
Packing Options
- In Bundles: Pipes are bundled together for ease of handling and transportation.
- In Loose: Individual pipes are packed loosely for flexible handling.
- Nylon Strip for Each Bundle/Piece Pipe: Secures each bundle or individual pipe to prevent damage during transit.
Key Benefits
- Enhanced Corrosion Resistance: The three-layer coating system provides superior protection against corrosion, extending the service life of the pipeline.
- Mechanical Strength: The polyethylene outer layer safeguards the pipe against mechanical damage during handling, installation, and operation.
- Strong Adhesion: The adhesive layer ensures robust bonding between the epoxy and polyethylene layers, preventing delamination.
- Compliance with Standards: Adherence to international standards ensures reliability and performance in various industrial applications.
Typical Applications
Coal Mine
- Usage: Transporting water, slurry, and other fluids in mining operations.
- Benefits: Reduces maintenance costs and downtime due to its excellent corrosion resistance.
Heat and Power Plant
- Usage: Carrying cooling water, steam, and other fluids essential for power generation.
- Benefits: Withstands high temperatures and harsh conditions, ensuring efficient operation.
Oil and Gas Transmission
- Usage: Transporting crude oil, natural gas, and refined products over long distances.
- Benefits: Provides a reliable and durable solution for pipeline infrastructure, withstanding environmental and mechanical stresses.
The 3PE coating pipe is an ideal choice for industries requiring durable and reliable pipeline solutions. Its multi-layered coating system offers exceptional corrosion resistance and mechanical protection, ensuring long-term performance and reduced maintenance costs. By adhering to international standards, these pipes provide a dependable solution for critical infrastructure in coal mines, power plants, and oil and gas transmission.