Galvanized Square and Rectangular Steel Pipes
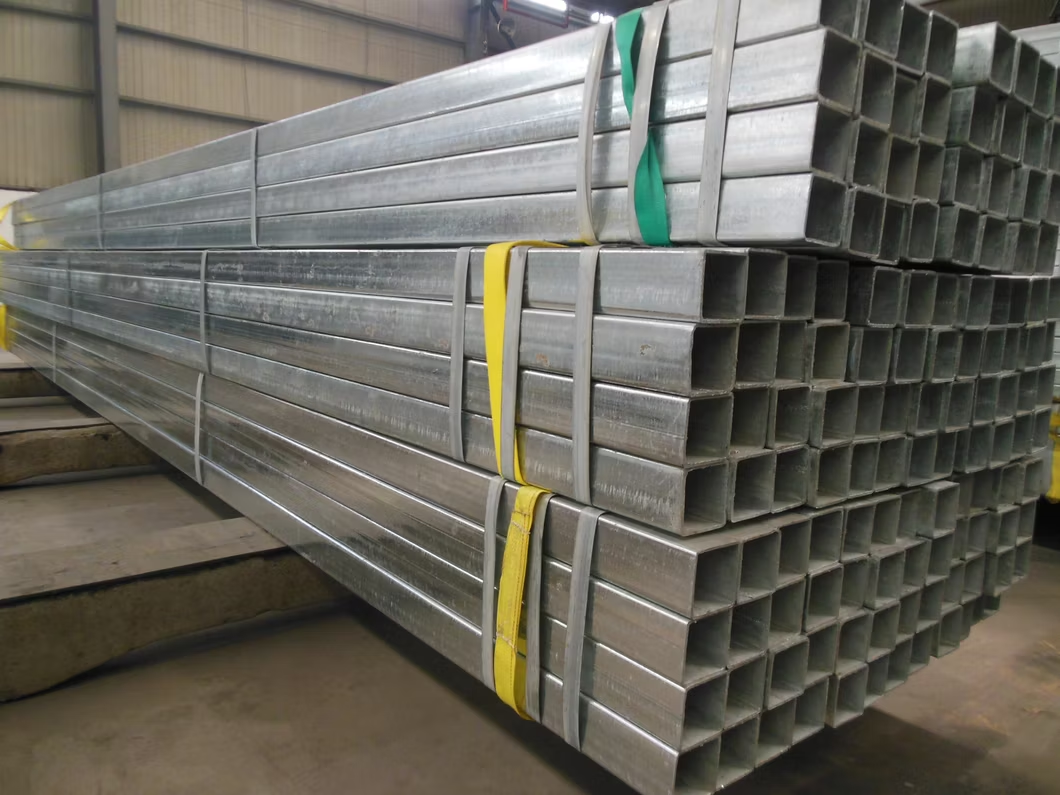
Comprehensive Guide to Galvanized Square and Rectangular Steel Pipes
Introduction
Galvanized square and rectangular steel pipes are essential components in various construction, industrial, and structural applications. These pipes are known for their durability, strength, and resistance to corrosion, making them ideal for both indoor and outdoor use. The galvanization process involves coating the steel pipes with a layer of zinc, which provides protection against rust and corrosion, significantly extending the lifespan of the pipes.
In this comprehensive guide, we will explore the key features, benefits, manufacturing processes, and applications of galvanized square and rectangular steel pipes. Additionally, we will delve into the different types of galvanization, the standards and specifications for these pipes, and the factors to consider when selecting the right pipes for your project. This article will also include detailed tables summarizing the technical specifications, dimensions, and weight of galvanized square and rectangular steel pipes.
What Are Galvanized Square and Rectangular Steel Pipes?
Galvanized square and rectangular steel pipes are hollow structural sections (HSS) that are coated with a layer of zinc to protect them from corrosion. These pipes are available in various sizes and thicknesses, making them suitable for a wide range of applications. The square and rectangular shapes provide excellent structural integrity and load-bearing capacity, making them ideal for use in construction, infrastructure, and industrial projects.
Key Features of Galvanized Square and Rectangular Steel Pipes:
- Corrosion Resistance: The zinc coating provides a protective barrier that prevents rust and corrosion, making these pipes suitable for outdoor and harsh environments.
- Durability: Galvanized steel pipes are highly durable and can withstand heavy loads and extreme weather conditions.
- Versatility: Available in various sizes, thicknesses, and lengths, galvanized square and rectangular steel pipes can be used in a wide range of applications.
- Cost-Effective: The galvanization process extends the lifespan of the pipes, reducing the need for frequent replacements and maintenance, making them a cost-effective solution in the long run.
- Aesthetic Appeal: The shiny, smooth surface of galvanized pipes gives them an attractive appearance, making them suitable for architectural and decorative applications.
Types of Galvanization
There are two primary methods of galvanizing steel pipes: hot-dip galvanization and pre-galvanization. Each method has its own advantages and is suitable for different applications.
1. Hot-Dip Galvanization
Hot-dip galvanization is the most common method of galvanizing steel pipes. In this process, the steel pipes are immersed in a bath of molten zinc at a temperature of around 450°C (842°F). The zinc reacts with the steel to form a metallurgical bond, creating a thick, durable coating that provides excellent corrosion resistance.
- Advantages:
- Provides a thick, uniform coating that offers superior corrosion protection.
- Suitable for outdoor and harsh environments.
- Long-lasting and requires minimal maintenance.
- Disadvantages:
- The process can result in a slightly rough surface finish.
- The zinc coating may be thicker at certain points, leading to uneven surfaces.
2. Pre-Galvanization
Pre-galvanization involves galvanizing the steel coil or sheet before it is formed into pipes. The steel is passed through a zinc bath, and then the pipes are formed by rolling and welding the pre-galvanized steel. This method is typically used for smaller pipes and applications where a thinner zinc coating is sufficient.
- Advantages:
- Provides a smooth, uniform surface finish.
- Suitable for indoor and less corrosive environments.
- More cost-effective than hot-dip galvanization for certain applications.
- Disadvantages:
- The zinc coating is thinner than that of hot-dip galvanized pipes, making it less suitable for highly corrosive environments.
- The weld seam may not be fully protected by the zinc coating, leading to potential corrosion at the weld joint.
Table 1: Comparison of Hot-Dip Galvanization and Pre-Galvanization
Feature | Hot-Dip Galvanization | Pre-Galvanization |
---|---|---|
Coating Thickness | Thick, uniform coating (up to 100 µm or more) | Thinner coating (typically 20-50 µm) |
Corrosion Resistance | Excellent for outdoor and harsh environments | Suitable for indoor and less corrosive environments |
Surface Finish | Slightly rough, may have uneven thickness | Smooth, uniform finish |
Cost | Higher cost due to thicker coating and process | More cost-effective for certain applications |
Applications | Outdoor structures, infrastructure, heavy-duty use | Indoor applications, light-duty use |
Standards and Specifications for Galvanized Steel Pipes
Galvanized square and rectangular steel pipes are manufactured according to various international standards to ensure quality, strength, and durability. These standards specify the dimensions, mechanical properties, and coating thickness of the pipes.
Common Standards for Galvanized Steel Pipes:
- ASTM A500: This standard covers cold-formed welded and seamless carbon steel structural tubing in round, square, and rectangular shapes. It specifies the mechanical properties and dimensions of the steel pipes.
- ASTM A53: This standard covers black and hot-dipped galvanized welded and seamless steel pipes for use in mechanical and pressure applications.
- EN 10219: This European standard specifies the technical delivery conditions for cold-formed welded structural hollow sections of non-alloy and fine-grain steels.
- JIS G3466: This Japanese standard covers carbon steel square and rectangular pipes for general structural purposes.
Table 2: Common Standards for Galvanized Square and Rectangular Steel Pipes
Standard | Description | Applications |
---|---|---|
ASTM A500 | Cold-formed welded and seamless carbon steel structural tubing | Structural applications, construction, infrastructure |
ASTM A53 | Black and hot-dipped galvanized welded and seamless steel pipes | Mechanical and pressure applications, plumbing, HVAC |
EN 10219 | Cold-formed welded structural hollow sections of non-alloy and fine-grain steels | Structural applications, building frameworks |
JIS G3466 | Carbon steel square and rectangular pipes for general structural purposes | General structural applications, construction, scaffolding |
Dimensions and Weight of Galvanized Square and Rectangular Steel Pipes
The dimensions and weight of galvanized square and rectangular steel pipes vary depending on the size, thickness, and length of the pipes. The size of the pipes is typically specified by the outer dimensions (OD) and wall thickness (WT).
Table 3: Dimensions and Weight of Galvanized Square Steel Pipes
Outer Dimension (OD) | Wall Thickness (WT) | Weight per Meter (kg/m) |
---|---|---|
20mm x 20mm | 1.2mm | 0.889 kg/m |
25mm x 25mm | 1.5mm | 1.47 kg/m |
30mm x 30mm | 2.0mm | 2.26 kg/m |
40mm x 40mm | 2.5mm | 3.53 kg/m |
50mm x 50mm | 3.0mm | 5.31 kg/m |
60mm x 60mm | 3.5mm | 7.25 kg/m |
80mm x 80mm | 4.0mm | 10.06 kg/m |
100mm x 100mm | 5.0mm | 15.29 kg/m |
Table 4: Dimensions and Weight of Galvanized Rectangular Steel Pipes
Outer Dimension (OD) | Wall Thickness (WT) | Weight per Meter (kg/m) |
---|---|---|
40mm x 20mm | 1.2mm | 1.18 kg/m |
50mm x 25mm | 1.5mm | 2.12 kg/m |
60mm x 30mm | 2.0mm | 3.14 kg/m |
80mm x 40mm | 2.5mm | 5.06 kg/m |
100mm x 50mm | 3.0mm | 7.85 kg/m |
120mm x 60mm | 3.5mm | 10.78 kg/m |
150mm x 100mm | 4.0mm | 15.29 kg/m |
200mm x 100mm | 5.0mm | 22.94 kg/m |
Manufacturing Process of Galvanized Steel Pipes
The manufacturing process of galvanized square and rectangular steel pipes involves several steps, including forming, welding, and galvanizing. The process may vary slightly depending on whether the pipes are hot-dip galvanized or pre-galvanized.
1. Forming and Welding
The first step in the manufacturing process is forming the steel into the desired shape. For square and rectangular pipes, the steel is typically cold-formed into the required dimensions. The edges of the steel are then welded together using high-frequency welding (HFW) or electric resistance welding (ERW) to create a continuous pipe.
2. Galvanization
Once the pipes are formed and welded, they are galvanized using either the hot-dip galvanization or pre-galvanization method. In hot-dip galvanization, the pipes are immersed in a bath of molten zinc, which forms a metallurgical bond with the steel. In pre-galvanization, the steel is galvanized before it is formed into pipes.
3. Inspection and Testing
After galvanization, the pipes undergo a series of inspections and tests to ensure they meet the required standards and specifications. These tests may include visual inspections, thickness measurements, and mechanical tests to verify the strength and durability of the pipes.
4. Cutting and Packaging
The final step in the manufacturing process is cutting the pipes to the required length and packaging them for shipment. The pipes are typically cut to standard lengths, such as 6 meters or 12 meters, but custom lengths can also be produced based on customer requirements.
Applications of Galvanized Square and Rectangular Steel Pipes
Galvanized square and rectangular steel pipes are used in a wide range of industries and applications due to their strength, durability, and corrosion resistance. Some of the most common applications include:
1. Construction and Infrastructure
In the construction industry, galvanized square and rectangular steel pipes are used for structural purposes, such as building frameworks, support columns, and beams. The corrosion resistance of galvanized pipes makes them ideal for outdoor structures, including bridges, fences, and guardrails.
2. Industrial Applications
In industrial settings, galvanized steel pipes are used for various purposes, including the transportation of fluids and gases, as well as for mechanical and pressure applications. The durability and strength of galvanized pipes make them suitable for high-pressure environments, such as oil and gas pipelines, chemical processing plants, and power plants.
3. Automotive Industry
In the automotive industry, galvanized steel pipes are used in the manufacturing of vehicle frames, exhaust systems, and other structural components. The corrosion resistance of galvanized pipes helps extend the lifespan of these components, particularly in environments where the vehicle is exposed to moisture and road salt.
4. Agriculture and Fencing
In agriculture, galvanized square and rectangular steel pipes are used for fencing, gates, and other structural applications. The corrosion resistance of galvanized pipes makes them ideal for use in outdoor environments, where they are exposed to moisture, soil, and chemicals.
5. Furniture and Decorative Applications
In furniture manufacturing and decorative applications, galvanized steel pipes are used to create modern, industrial-style furniture, such as tables, chairs, and shelving units. The smooth, shiny surface of galvanized pipes gives them an attractive appearance, making them suitable for both functional and decorative purposes.
6. Solar Energy Systems
In solar energy systems, galvanized square and rectangular steel pipes are used to construct the frames and supports for solar panels. The strength and corrosion resistance of galvanized pipes make them ideal for use in outdoor solar installations, where they are exposed to the elements.
Table 5: Common Applications of Galvanized Square and Rectangular Steel Pipes
Industry | Application |
---|---|
Construction | Building frameworks, support columns, beams, outdoor structures |
Industrial | Fluid and gas transportation, mechanical and pressure applications |
Automotive | Vehicle frames, exhaust systems, structural components |
Agriculture | Fencing, gates, outdoor structures |
Furniture and Decorative | Industrial-style furniture, tables, chairs, shelving units |
Solar Energy | Frames and supports for solar panels |
Factors to Consider When Selecting Galvanized Steel Pipes
When selecting galvanized square and rectangular steel pipes for your project, there are several factors to consider to ensure you choose the right pipes for your specific application.
1. Size and Dimensions
The size and dimensions of the pipes are critical factors to consider, as they determine the load-bearing capacity and structural integrity of the pipes. The outer dimensions (OD) and wall thickness (WT) should be selected based on the specific requirements of your project.
2. Coating Thickness
The thickness of the zinc coating is an important factor in determining the corrosion resistance of the pipes. For outdoor and harsh environments, pipes with a thicker zinc coating (such as those produced by hot-dip galvanization) are recommended. For indoor applications, pipes with a thinner coating (such as pre-galvanized pipes) may be sufficient.
3. Mechanical Properties
The mechanical properties of the pipes, such as tensile strength, yield strength, and elongation, should be considered based on the load and stress the pipes will be subjected to. Pipes manufactured according to standards such as ASTM A500 and EN 10219 provide specific mechanical properties that ensure the pipes can withstand the required loads.
4. Corrosion Resistance
The level of corrosion resistance required for your project will depend on the environment in which the pipes will be used. For outdoor and corrosive environments, hot-dip galvanized pipes with a thick zinc coating are recommended. For indoor or less corrosive environments, pre-galvanized pipes may be sufficient.
5. Cost
The cost of galvanized steel pipes can vary depending on the size, coating thickness, and manufacturing method. While hot-dip galvanized pipes may have a higher initial cost, their longer lifespan and reduced maintenance requirements can make them more cost-effective in the long run.
Table 6: Factors to Consider When Selecting Galvanized Steel Pipes
Factor | Considerations |
---|---|
Size and Dimensions | Select the appropriate outer dimensions (OD) and wall thickness (WT) based on load requirements |
Coating Thickness | Choose a thicker zinc coating for outdoor and harsh environments |
Mechanical Properties | Ensure the pipes meet the required tensile strength, yield strength, and elongation |
Corrosion Resistance | Select pipes with the appropriate level of corrosion resistance for the environment |
Cost | Consider the long-term cost-effectiveness of hot-dip galvanized pipes |
Conclusion
Galvanized square and rectangular steel pipes are versatile, durable, and corrosion-resistant, making them an ideal choice for a wide range of applications. Whether used in construction, industrial settings, automotive manufacturing, or decorative applications, these pipes provide the strength and longevity needed for both indoor and outdoor environments.
FAQ
What is the difference between hot-dip galvanization and pre-galvanization?
Hot-dip galvanization involves immersing the steel pipes in a bath of molten zinc, creating a thick, durable coating that provides excellent corrosion resistance. Pre-galvanization, on the other hand, involves galvanizing the steel before it is formed into pipes, resulting in a thinner zinc coating. Hot-dip galvanized pipes are better suited for outdoor and harsh environments, while pre-galvanized pipes are suitable for indoor and less corrosive environments.
What are the common applications of galvanized square and rectangular steel pipes?
Galvanized square and rectangular steel pipes are used in a wide range of applications, including construction (building frameworks, support columns), industrial (fluid and gas transportation), automotive (vehicle frames, exhaust systems), agriculture (fencing, gates), furniture (industrial-style furniture), and solar energy systems (frames and supports for solar panels).
What standards are used for galvanized steel pipes?
Common standards for galvanized steel pipes include ASTM A500 (cold-formed welded and seamless carbon steel structural tubing), ASTM A53 (black and hot-dipped galvanized welded and seamless steel pipes), EN 10219 (cold-formed welded structural hollow sections), and JIS G3466 (carbon steel square and rectangular pipes for general structural purposes).
How do I choose the right galvanized steel pipe for my project?
When selecting galvanized steel pipes, consider factors such as the size and dimensions, coating thickness, mechanical properties, corrosion resistance, and cost. The specific requirements of your project, such as the load-bearing capacity and environmental conditions, will determine the most suitable pipe for your application.
What is the lifespan of galvanized steel pipes?
The lifespan of galvanized steel pipes depends on the thickness of the zinc coating and the environment in which they are used. Hot-dip galvanized pipes with a thick zinc coating can last up to 50 years or more in outdoor environments, while pre-galvanized pipes with a thinner coating may have a shorter lifespan in corrosive environments.