Galvanized Steel Hollow Section
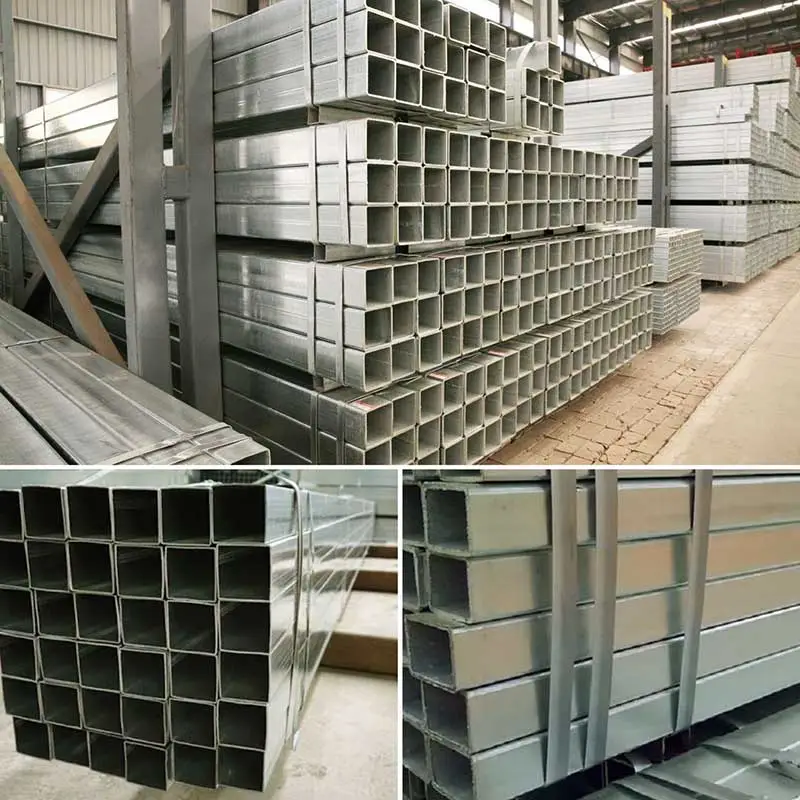
Material Grade
|
Standard
|
Description
|
---|---|---|
Gr.A, Gr.B, Gr.C
|
ASTM A500, ASTM A53
|
Carbon steel grades with varying tensile and yield strengths for structural use
|
S275J0H
|
EN10219
|
Structural steel with minimum yield strength of 275 MPa, cold-formed
|
S355JR
|
EN10219
|
Higher strength steel (355 MPa yield), suitable for structural applications
|
S355J0H
|
EN10219
|
Cold-formed structural steel with 355 MPa yield strength
|
S355J2H
|
EN10219
|
Enhanced toughness steel for low-temperature applications
|
A36
|
ASTM A36
|
Low carbon steel with good weldability and formability
|
SS400
|
JIS G3101
|
General-purpose structural steel, equivalent to mild steel
|
Q195
|
GB/T 13793-1992
|
Low carbon steel with basic strength, used in light structural applications
|
Q235
|
GB/T 13793-1992
|
Mild steel with moderate strength, widely used in construction
|
Q345
|
GB/T 13793-1992
|
High-strength low-alloy steel, equivalent to S355 grades
|
-
Gr.A, Gr.B, Gr.C (ASTM A500): These grades differ in yield strength (e.g., Gr.A: 230 MPa, Gr.B: 315 MPa, Gr.C: 345 MPa) and are used for structural tubing.
-
S275J0H, S355JR, S355J0H, S355J2H (EN10219): European grades with specified impact toughness and yield strengths, ideal for hollow sections.
-
A36: Yield strength of 250 MPa, commonly used in the U.S. for structural purposes.
-
SS400: Yield strength of 245 MPa, a Japanese standard steel with excellent ductility.
-
Q195, Q235, Q345: Chinese grades with increasing strength (Q195: 195 MPa, Q235: 235 MPa, Q345: 345 MPa).
-
ASTM A500: Specifies cold-formed welded and seamless carbon steel structural tubing.
-
ASTM A53: Covers seamless and welded steel pipes, often galvanized for corrosion resistance.
-
API 5L: Standards for line pipes, applicable to oil and gas industries.
-
BS1387: British standard for welded steel tubes, often galvanized.
-
EN39: Specifies steel tubes for scaffolding.
-
JIS 3466: Japanese standard for rectangular structural steel tubes.
-
EN10219: European standard for cold-formed welded structural hollow sections.
-
GB/T 13793-1992: Chinese standard for welded steel pipes.
-
Process Steps:
-
Surface Preparation: Steel is cleaned via degreasing, pickling (acid bath), and fluxing (zinc ammonium chloride solution) to remove rust, oil, and impurities.
-
Immersion: The cleaned steel is dipped into molten zinc, typically at 440-460°C.
-
Cooling: The coated steel is withdrawn and cooled in air or water, forming a crystalline zinc surface.
-
Inspection: Coating thickness and uniformity are checked.
-
-
Coating Thickness: Typically ranges from 40-600 g/m² (depending on standards and requirements), equivalent to 5-85 µm per side.
-
Advantages:
-
Thick, durable coating with excellent corrosion resistance.
-
Self-healing properties due to zinc’s sacrificial anodic behavior.
-
-
Disadvantages:
-
Higher cost and energy consumption.
-
Potential for uneven coating on complex shapes.
-
-
Process Steps:
-
Surface Preparation: Steel is cleaned to remove dirt, grease, and rust (e.g., sandblasting to Sa2.5 standard).
-
Application: Zinc-rich paint is applied using a spray gun, brush, or roller.
-
Curing: The coating dries at ambient temperature, forming a protective layer.
-
Inspection: Coating adhesion and thickness are verified.
-
-
Coating Thickness: Typically 20-80 µm, thinner than hot-dip galvanizing.
-
Advantages:
-
Lower cost and simpler application.
-
Suitable for on-site repairs or small components.
-
-
Disadvantages:
-
Less durable than hot-dip galvanizing.
-
No metallurgical bonding, reducing long-term corrosion resistance.
-
Parameter
|
Hot-Dip Galvanizing
|
Cold Galvanizing
|
---|---|---|
Zinc Application
|
Molten zinc bath
|
Zinc-rich paint
|
Coating Thickness
|
40-600 g/m² (5-85 µm/side)
|
20-80 µm
|
Bonding
|
Metallurgical (zinc-iron alloy)
|
Mechanical (paint adhesion)
|
Corrosion Resistance
|
High
|
Moderate
|
Cost
|
Higher
|
Lower
|
Application
|
Factory-based
|
On-site or factory
|
Durability
|
20-50 years
|
5-15 years
|
-
Process:
-
Billet Preparation: A solid steel billet (e.g., Q235 or S355JR) is heated to 1200-1300°C.
-
Piercing: The billet is pierced using a mandrel to form a hollow tube.
-
Rolling: The tube is elongated and shaped via hot rolling.
-
Sizing: Final dimensions are achieved through cold drawing or sizing rolls.
-
-
Standards: ASTM A53, API 5L.
-
Advantages: Higher strength and no weld seam weaknesses.
-
Process:
-
Strip Preparation: Steel coils (e.g., SS400 or Q345) are slit into strips.
-
Forming: Strips are cold-formed into a round shape using rollers (ERW process) or bent into rectangular/square shapes (JIS 3466).
-
Welding: Edges are welded using high-frequency electric resistance welding (ERW) or submerged arc welding (SAW).
-
Shaping: For rectangular/square sections, the round tube is further formed into the desired shape.
-
Galvanizing: Applied post-forming (hot-dip) or pre-galvanized strips are used.
-
-
Standards: ASTM A500, EN10219, BS1387.
-
Advantages: Cost-effective and suitable for mass production.
-
Pre-Galvanized: Steel strips are galvanized before forming. Weld seams may lack zinc coating unless touched up.
-
Post-Galvanized: Entire section is galvanized after forming, ensuring uniform coating.
Parameter
|
Round Pipe
|
Rectangular Pipe
|
Square Pipe
|
---|---|---|---|
Outer Diameter (OD)
|
12.7-609 mm
|
N/A
|
N/A
|
Width x Height
|
N/A
|
10×15 to 800×1200 mm
|
10×10 to 1200×1200 mm
|
Wall Thickness (WT)
|
0.5-60 mm
|
0.5-60 mm
|
0.5-60 mm
|
Length
|
0.5-26.5 m (customizable)
|
0.5-26.5 m (customizable)
|
0.5-26.5 m (customizable)
|
Zinc Coating
|
40-600 g/m²
|
40-600 g/m²
|
40-600 g/m²
|
Standards
|
ASTM A500, A53, BS1387
|
EN10219, JIS 3466
|
EN10219, JIS 3466
|
-
Tolerances:
-
OD: ±1% (ASTM A500).
-
WT: ±10% (EN10219).
-
Length: ±50 mm or as specified.
-
-
Visual Inspection:
-
Check for surface defects (cracks, dents) and zinc coating uniformity.
-
-
Coating Thickness Test:
-
Magnetic gauge or micrometer to measure zinc thickness (e.g., ASTM A123 requires 45-85 µm for structural steel).
-
-
Dimensional Check:
-
Verify OD, WT, length, and straightness using calipers, rulers, or laser systems.
-
-
Mechanical Testing:
-
Tensile test (yield strength, elongation per ASTM A500).
-
Bend test (ductility).
-
-
Corrosion Resistance:
-
Salt spray test (ASTM B117) to assess zinc coating durability.
-
-
Weld Integrity:
-
Ultrasonic testing (UT) or X-ray for welded sections.
-
Test
|
Standard
|
Requirement
|
---|---|---|
Zinc Coating Thickness
|
ASTM A123
|
40-600 g/m² (varies by thickness)
|
Tensile Strength
|
ASTM A500
|
Gr.B: 315 MPa min
|
Yield Strength
|
EN10219
|
S355J2H: 355 MPa min
|
Weld Seam
|
BS1387
|
No visible cracks or porosity
|
Corrosion Test
|
ASTM B117
|
500-1000 hours without red rust
|
-
Raw Material Selection: Choose appropriate steel grade (e.g., Q235, S355JR).
-
Forming: Seamless or welded process to create hollow sections.
-
Galvanizing: Hot-dip or cold galvanizing applied.
-
Cutting: Pipes cut to specified lengths using saws or plasma cutters.
-
End Finishing: Plain ends, beveled (30-35°), or threaded (BS1387).
-
Surface Treatment: Optional painting or additional coatings (e.g., 3LPE).
-
Packaging: Bundled or crated for transport.
-
Applications: Water supply, gas pipelines, scaffolding (BS1387, EN39).
-
Sizes: OD 12.7-609 mm, WT 0.5-60 mm.
-
Features: High pressure resistance, easy threading.
-
Processing: Often ERW welded, then hot-dip galvanized.
-
Applications: Structural frameworks, fencing, furniture (EN10219, JIS 3466).
-
Sizes: 10×15 to 800×1200 mm, WT 0.5-60 mm.
-
Features: High load-bearing capacity in one direction.
-
Processing: Formed from round tubes, galvanized post-forming.
-
Applications: Building columns, machinery frames (EN10219, JIS 3466).
-
Sizes: 10×10 to 1200×1200 mm, WT 0.5-60 mm.
-
Features: Uniform strength in all directions.
-
Processing: Similar to rectangular, with precise corner radii.