HOW TO CHOOSE THE RIGHT HEAT EXCHANGER TUBES
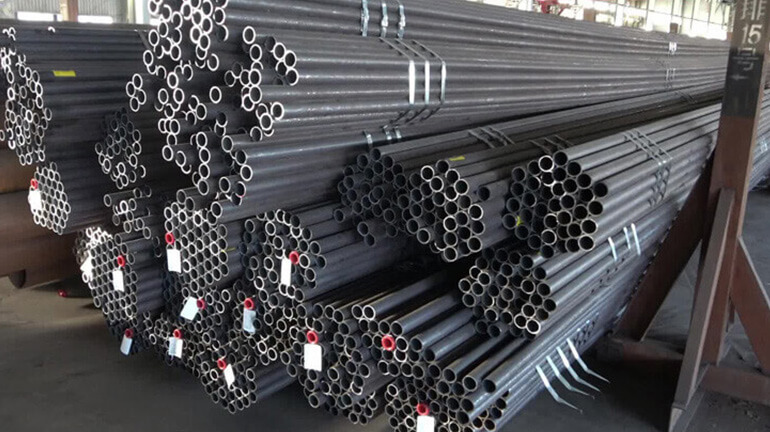
Heat Exchanger Tube Selection Criteria: How to Choose the Right Heat Exchanger Tubes
Introduction
Heat exchangers are critical components in various industrial processes, responsible for transferring heat between two or more fluids. The selection of appropriate heat exchanger tubes is paramount for ensuring efficiency, longevity, and performance. This guide provides comprehensive criteria for selecting the right heat exchanger tubes.
1. Understanding Heat Exchanger Tubes
1.1 Function of Heat Exchanger Tubes
Heat exchanger tubes facilitate the transfer of thermal energy between fluids while preventing direct mixing. The design and material of the tubes significantly affect the heat transfer efficiency and pressure drop.
1.2 Types of Heat Exchanger Tubes
- Straight Tubes: Common in shell and tube heat exchangers.
- U-Tubes: Allow for thermal expansion and contraction.
- Finned Tubes: Enhance heat transfer rates by increasing surface area.
2. Key Selection Criteria
2.1 Material Selection
Material selection is crucial for durability and performance. Consider the following factors:
- Corrosion Resistance: Choose materials that can withstand the specific fluids involved.
- Thermal Conductivity: Higher conductivity materials improve heat transfer.
- Mechanical Strength: Ensure the material can handle the operating pressures and temperatures.
Common Materials
- Stainless Steel: Excellent corrosion resistance and thermal conductivity.
- Copper: High thermal conductivity, but less corrosion-resistant.
- Alloys: Specialized for extreme conditions, such as high temperatures or corrosive environments.
2.2 Tube Diameter and Length
The diameter and length of the tubes impact the overall heat transfer area and pressure drop.
- Diameter: Larger diameters generally reduce flow resistance but may require more space.
- Length: Longer tubes increase heat transfer area but can also increase pressure drop.
2.3 Heat Transfer Requirements
Evaluate the heat transfer rate needed for your application. This can be calculated using:
�=�×�×Δ�
Where:
- � = heat transfer rate
- � = overall heat transfer coefficient
- � = heat transfer area
- Δ� = temperature difference
2.4 Flow Arrangement
The flow arrangement affects heat transfer efficiency:
- Counterflow: Fluids flow in opposite directions, maximizing temperature difference.
- Parallel Flow: Fluids flow in the same direction, less efficient than counterflow.
- Crossflow: Fluids move perpendicular to each other, commonly used in air-cooled exchangers.
2.5 Pressure Drop Considerations
Minimizing pressure drop is essential for energy efficiency. The design of the tubes, including diameter and length, affects the flow resistance.
2.6 Operating Conditions
Understand the operating conditions, including:
- Temperature: Ensure materials can withstand maximum temperatures.
- Pressure: Select tubes that can handle the maximum operating pressure.
- Fluid Properties: Consider viscosity, density, and flow rates of the fluids involved.
2.7 Manufacturing Processes
Different manufacturing processes affect the final properties of the tubes:
- Seamless Tubes: Offer higher strength and corrosion resistance.
- Welded Tubes: Generally less expensive but may have lower mechanical properties.
2.8 Regulatory Compliance
Ensure that selected materials and designs comply with industry standards and regulations, such as ASME, TEMA, and API.
3. Performance Testing
3.1 Non-Destructive Testing (NDT)
Implement NDT methods to assess the integrity of the tubes without causing damage. Common methods include:
- Ultrasonic Testing: Detects internal flaws.
- Radiographic Testing: Uses X-rays to inspect welds and joints.
3.2 Performance Evaluation
Conduct performance tests under simulated operational conditions to evaluate efficiency and durability.
4. Maintenance Considerations
4.1 Cleaning and Maintenance
Choose materials and designs that allow for easy cleaning, especially in applications prone to fouling.
4.2 Inspection Protocols
Establish regular inspection protocols to identify wear and tear or corrosion before they lead to failures.
5. Conclusion
Selecting the right heat exchanger tubes involves a careful evaluation of various criteria, including material properties, design specifications, operating conditions, and maintenance needs. By following these guidelines, you can enhance the efficiency and longevity of your heat exchangers, ultimately improving the performance of your industrial processes.
6. References
- TEMA (Tubular Exchanger Manufacturers Association) Standards
- ASME (American Society of Mechanical Engineers) Boiler and Pressure Vessel Code
- API (American Petroleum Institute) Standards
7. Detailed Analysis of Tube Materials
7.1 Stainless Steel
Properties:
- High corrosion resistance.
- Good thermal conductivity.
- Strength at elevated temperatures.
Applications:
- Suitable for a wide range of fluids, including water, oils, and chemicals.
Considerations:
- Cost may be higher compared to other materials.
- Requires careful selection of grade (e.g., 304, 316) based on fluid compatibility.
7.2 Copper
Properties:
- Excellent thermal conductivity (higher than stainless steel).
- Antimicrobial properties.
Applications:
- Ideal for heating and cooling applications, such as in HVAC systems.
Considerations:
- Prone to corrosion in certain environments, particularly with chlorides.
- Typically used in smaller systems due to cost and weight.
7.3 Alloys
Properties:
- Designed for specific conditions (e.g., high temperature, high pressure, corrosive fluids).
Applications:
- Used in petrochemical industries and power plants.
Considerations:
- More expensive and often requires specialized welding techniques.
8. Designing for Efficiency
8.1 Enhancing Heat Transfer
Finned Tubes
- Description: Tubes with fins attached to increase surface area.
- Benefits: Improved heat transfer efficiency, especially in gas-to-liquid applications.
Tube Geometry
- Twisted Tubes: Enhance turbulence and increase heat transfer.
- Corrugated Tubes: Increase surface area and improve flow characteristics.
8.2 Minimizing Fouling
- Material Selection: Use materials that resist fouling (e.g., smooth surfaces).
- Regular Maintenance: Implement cleaning schedules to prevent buildup.
9. Cost Considerations
9.1 Initial Costs vs. Long-Term Savings
- Material Costs: Higher initial costs for corrosion-resistant materials may lead to savings in maintenance and replacement.
- Energy Costs: Efficient heat exchangers reduce energy consumption, impacting overall operational costs.
9.2 Life Cycle Cost Analysis
Conduct a life cycle cost analysis (LCCA) to evaluate the total cost of ownership, including installation, maintenance, and operational costs over the expected lifespan of the heat exchanger.
10. Case Studies
10.1 Case Study 1: Chemical Processing Plant
Challenge: High corrosion rates in existing heat exchangers.
Solution: Upgraded to titanium tubes, enhancing corrosion resistance and reducing downtime for maintenance.
Outcome: Increased operational efficiency and reduced maintenance costs.
10.2 Case Study 2: HVAC System
Challenge: Inefficient heat transfer leading to high energy bills.
Solution: Implemented finned copper tubes to enhance heat transfer.
Outcome: Achieved a 20% reduction in energy consumption.
11. Future Trends
11.1 Advanced Materials
Research into new materials, such as nanomaterials and composites, promises improved performance in extreme conditions.
11.2 Smart Heat Exchangers
Integration of IoT technology allows for real-time monitoring of performance, enabling predictive maintenance and optimizing efficiency.
11.3 Sustainability Considerations
Focus on selecting materials and processes that minimize environmental impact, including recyclability and energy efficiency.
13. References
- TEMA (Tubular Exchanger Manufacturers Association) Standards
- ASME (American Society of Mechanical Engineers) Guidelines
- API (American Petroleum Institute) Best Practices
- Recent Research Articles on Heat Exchanger Efficiency