Research progress and prospect of key technologies for High temperature and high pressure resistance line pipe steel and pipes
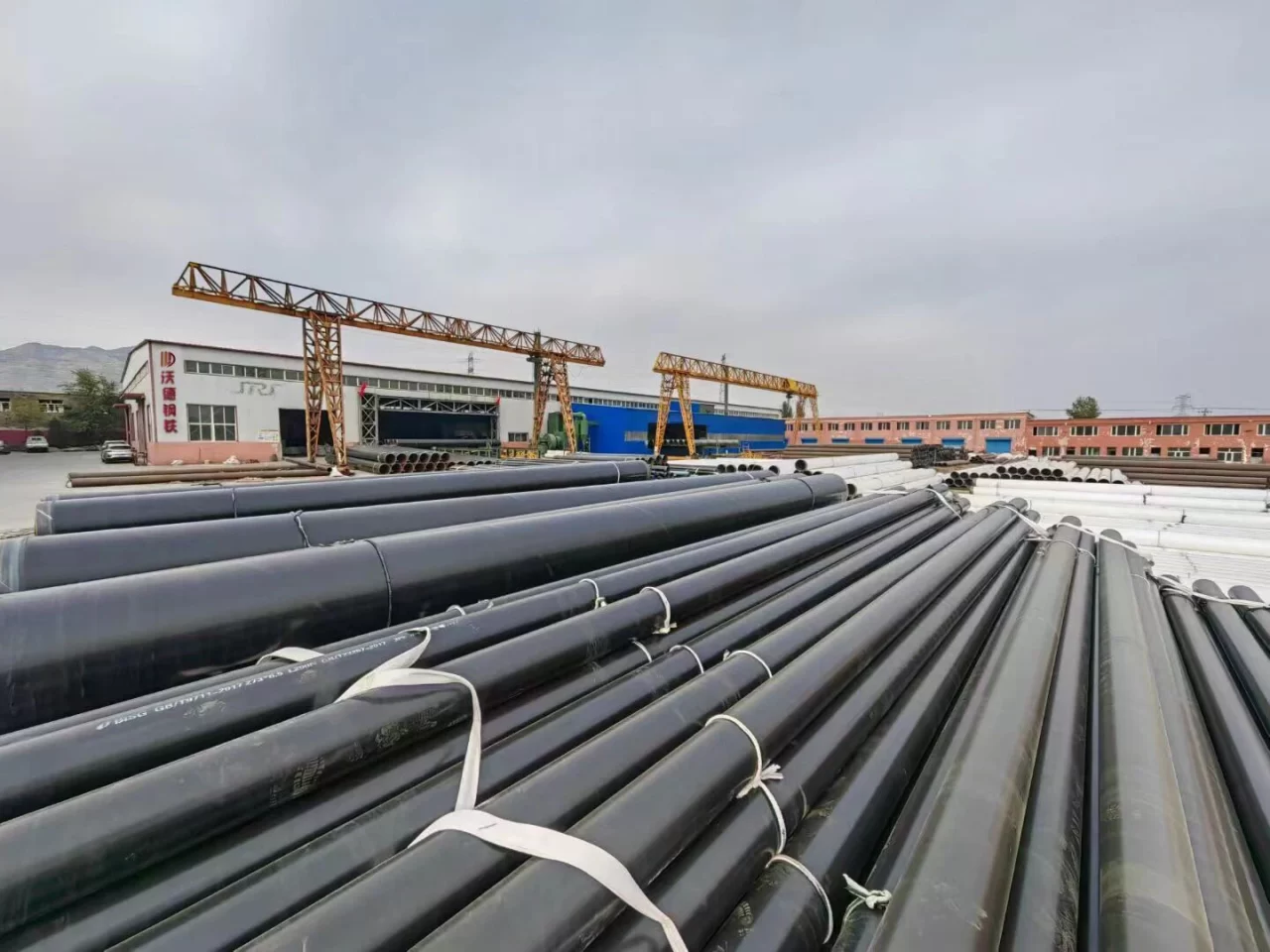
Introduction
As fossil fuel exploration becomes increasingly challenging through expanded deepwater drilling and unconventional shale plays, line pipes face ever more stringent operating requirements to safely transport fluids from these extreme reservoir conditions. While current carbon and alloy steels have served industry well for decades, next-generation “super steel” pipe designs capable of withstanding prolonged use at temperatures surpassing 300°C and pressures over 20,000 psi will be vital to cost-effective energy production. Considerable research efforts across science and engineering domains aim to understand and control material microstructures, optimize protective coatings, and advance non-destructive characterization techniques necessary for ultra-deep service pipelines. This report provides an in-depth review of the state of the art and future prospects across composition development, microstructure optimization, coating technologies, and non-destructive evaluation methodologies, with the goal of realizing true “fit-for-purpose” line pipes.
Steel Composition and Microstructure Optimization
Composition engineering underpins achieving the refined balance of strength, ductility, and thermal stability required of high-pressure line pipes at higher operating temperatures. Significant advances have been made in refining grain structures and precipitating stable secondary phases through judicious alloying additions alone or combined with thermomechanical processing routes.
Recent studies demonstrate notable hardening via additions of Nb and V that segregate to grain and subgrain boundaries as fine precipitates like NbC and VC, with increasing solubility at elevated temperatures maintaining strength without embrittlement. Beyond single elements, nano-scale complex carbide and carbonitride precipitates formed via additions of Mo, Nb and Ti are being explored, showing promise to strengthen both ferrite and austenite phases at once. Additional benefits of tailored non-metallic inclusions and oxide dispersions are emerging areas of research focus as well.
Dual-phase ferrite-martensite microstructures created through controlled heat treatment of low-carbon steels supplemented with Si and Mn particularly attract interest, displaying beneficial combinations of high strength and fracture toughness stable up to 300°C that may fulfill deepwater piping needs. Thermomechanical processing following approaches like quenching and partitioning expand the design space for microstructure-property optimization.
Nevertheless, a major challenge remains elucidating the exact relationships between changing alloy chemistry, precipitation behaviors, grain/phase morphologies, and mechanical properties as temperature increases, necessitating advancement of characterization techniques at high temperatures and computational modeling efforts informed by experimental data. Continued iteration is needed to design “super steel” compositions uniquely suited for long-term ultra-high pressure service scenarios with true enhanced temperature limits.
Coating and Cladding Technologies
Whether fusion-bonded epoxy, three-layer polyurethane, concrete coating, or advanced materials applied via cladding, surface engineering techniques undergo revolution to protect line pipes against internal and external corrosion threats at higher temperatures. Considerable progress strengthens organic coatings through additives that encourage self-healing of holidays and cracking: tests recently validated a leading commercial epoxy system’s integrity for 30+ years at 350°C.
Ceramic composite coatings applied using combustion spraying, plasma spraying, or physical/chemical vapor deposition address corrosion/erosion from water/sand/CO2 at higher temperatures far better than conventional organic choices. Current research centers around optimizing nano-structured composite layers with oxide/carbide reinforcements in matrices like aluminum or silicon to achieve defect-free, dense and adhesive coatings exhibiting thermal expansion matches to substrates and diffusional barrier functionality.
More radically, cladding techniques like laser engineered net shaping (LENS) enable deposition of centimeter-thick metallic or even functionally graded alloy wall sections featuring tailored compositions optimized for local corrosion/wear resistance, high temperature strength, and thermal insulation properties. Validation challenges involve demonstrating long-term durability, especially considering effects like residual stresses and galvanic/interfacial mechanisms during thermal cycling in extreme service conditions.
Overall the field progresses rapidly, though lengthy and careful in-service validation remains crucial before commercializing coatings and claddings for ultra-deep pipeline projects assuredly enduring decades at high pressures and temperatures. Multi-scale performance modeling and accelerated testing aid effective evaluation strategies.
Non-destructive Evaluation Techniques
Quality control and fitness-for-service assessment of complex line pipe designs require upgrading non-destructive testing capabilities. Advancing the ability to detect, size, and characterize defects invisible to conventional ultrasonic, radiographic, and magnetic techniques motivates development of advanced instrumentation for the manufacturing and operations stages as well as in-line inspections.
Guided-wave techniques concentrate ultrasonic wave modes along pipes for rapid full-length scanning, with current work striving to pinpoint anomalies below 1mm in diameter through modeling wave-structure interactions. In parallel, phased-array technology enhances sensitivity and resolution by electronically steering focused beams. Lab experiments demonstrate detection of 20um-diameter notches when combined with new diffraction analysis evaluations of amplitude/phase changes in received A-scan signals.
Computed radiography harnesses area detectors and machine learning pattern recognition to automatically segment and dimension subsurface anomalies often indistinguishable to human interpreters. Pulsed eddy current holds promise for high-resolution inspection of protective coatings and claddings where imperfections may degrade barrier functions. Advancements like shear-wave guided-Lamb waves and plane-wave ultrasonic testing open exciting new inspection windows as well for challenging pipe geometries.
As line pipes incorporate novel steels, coatings, and additive designs to unlock ultra-deep viability, corresponding non-destructive evaluation techniques require parallel innovations to enable truly fit-for-purpose qualification and defect-free integrity assessments from manufacturing through decades of service at extreme pressures over 300°C. Combined experimental and computational approaches drive progress.
Conclusion
Advancing line pipe designs for the most punishing high-pressure, high-temperature deep energy extraction applications demands an integrated, multi-disciplinary research and development approach. While significant gains have emerged across composition development, microstructure optimization, advanced surface engineering, and next-generation non-destructive testing methods, continued advancement relies on close synergies between materials scientists, mechanical engineers, corrosion experts, nondestructive evaluators and computational modeling specialists. Deeper understanding of interacting structure-processing-property relationships informs targeted design of unique “super steel” alloys and coatings tailored for ultra-harsh, long-term subsea and geothermal service conditions. Meanwhile, qualification and fitness-for-service protocols must evolve hand-in-hand leveraging the most cutting-edge inspection technology. Though a challenging endeavor, realizing true “fit-for-purpose” pipelines assures continued energy supply from even the harshest subsurface reservoirs, supporting worldwide energy security for decades to come.